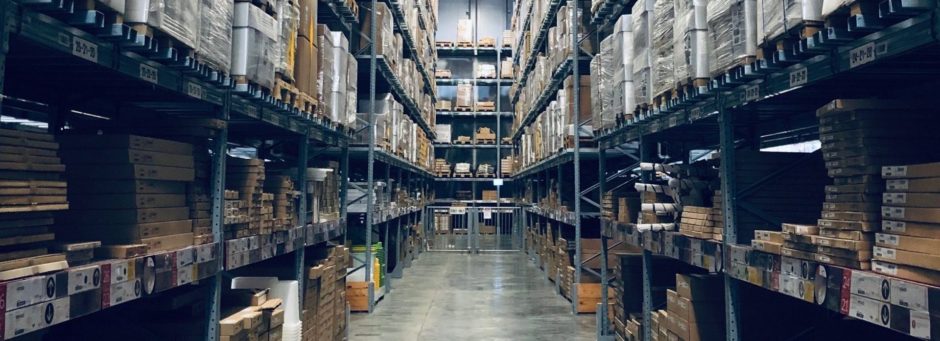
The Challenge:
The client, a leading medical supply company, during a period of expanding manufacturing into Asia combined with a dramatic increase in sales, experienced major supply chain disruption to their distribution network and supporting customers. Product availability plummeted causing lost sales, excessive expediting, increased transportation costs due to out-of-network shipments – overall shaking customer confidence.
Results:
Our team conducted a detailed value stream analysis and was able to identify several root causes effecting product availability. During the implementation phase, we worked with front line supervisors, operations managers, and executives to re-engineer processes and implement changes to roles and responsibilities, equipment and technology. As improvements were implemented, product availability improved week over week and sustained at 52% improvement over the base line period.
The new process involved changing the material handling equipment, updating Standard Operating Procedures, and training the employees. In addition, we developed metrics and standards to monitor and control the new process.
Highlights this client achieved include:
- Availability improved by 52%
- Improved warehouse productivity
- Improved inventory accuracy